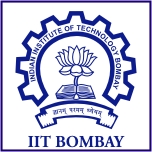
Friction stir welding (FSW) is a solid state joining technique. During FSW, workpieces are plastically deformed and mechanically intermixed under mechanical pressure at elevated temperatures. However, these joints are created below the solidus temperature of the workpiece. The ability of FSW process to join materials without melting allows the venues for welding/joining of dissimilar materials. The objective of this project is to investigate and model material mixing, intermetallic compound formation and diffusion during friction stir welding of dissimilar materials.
Department of Science & Technology
Incremental sheet forming is a dieless forming process, in which sheet is clamped at its periphery and a hemispherical tool is used to apply small incremental pressure to deform the sheet. The sum of these small incremental deformations leads to the required geometry of the sheet. The project is focused on understanding the deformation mechanism during this process. This involves the analyses of the microstructural aspects of the deformed sheet and finite element analysis of the stress and strain fields during the process.
Prof. K Narasimhan & Prof. Suhil Mishra, IIT Bombay
Joints of dissimilar materials provide venues for light weighting in many applications. Intermetallic compounds are inevitable in dissimilar material joints. The fatigue and fracture characteristics of dissimilar joints are of particular interest for the applications where joints are subjected to cyclic loading. The nature of intermetallic compound and its distribution determines the fatigue performance of the joint. The objective of this work is to map the intermetallic compound formation to the joining process parameters and to correlate the nature and distribution of compounds to the fatigue behaviour of the dissimilar joints.
Prof. Wenyi Yan, Monash University, Australia
IITB-Monash Research Academy
In order to expedite the quality checks on the finished parts, it is desirable to measure the internal and external geometric features in-line with part production. This project deals with development of X-ray based non-contact online measurement system, for internal and external geometries of the components.
Puretronics India
The work is focused on additive manufacturing with Titanium alloys and Inconel alloys. Currently, the interest is in understanding the effect of scanning strategies on the mechanical properties of the resulting deposits. Numerical tools are developed to predict the heat transfer, fluid flow and thermal history-based phase transformation during the process. Further investigations are underway to establish the structure-property relationships for the resulting deposits.
Titanium nanotubes on biomedical implant surfaces promote the osseointegration, cell differentiation, mineralisation and antibacterial properties. This project focuses on synthesis of high aspect ratio ordered Titania nanotubes on Titanium alloy. The effect of process parameters on the growth rate of the nanotubes is investigated. Further, the samples with varying geometries of nanotubes will be tested for cell growth.
Prof. Kamendra Sharma, IIT Bombay
Centre for Research in Nanotechnology & Science, IIT Bombay
Project Title | Duration | Sponsoring Agency |
---|---|---|
Vacuum Brazing of SS 321 and Silver components | 2018-19 | Brahmos Aerospace Private Limited |
Automation of Cable Manufacturing Process | 2017-19 | TE Connectivity India Private Limited |
Liquified Petroleum Gas Transfer | 2018-18 | Bharat Petroleum Corporation Limited |
Development of Magnetic Drilling Machine | 2016-18 | BroachCutter Drilling Machines Private Limited |