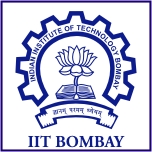
Welding Processes
Introduction to welding processes & technology: joining, fusion welding, solid state welding, mechanical joining, gas welding, electric arc welding, laser welding and electron beam welding. Fundamentals of fusion welding processes: heat source, analysis of heat flow in welding, fluid flow in melt pool and types of metal transfer. Chemical reactions in welding: gas-metal reactions and slag-metal reactions. Microstructure evolution: solidification mechanisms, effect of cooling rate, grain growth at fusion zone and fusion boundary, heat affected zone. Application: types of weld joint, residual stresses, distortion and fatigue, welding defects, destructive and non-destructive testing of welds.
Solid State Joining
Mechanisms of solid state joining: thermo-mechanical processing of metals and metal-alloys, diffusion in solids and adhesive models. Deformation based joining processes: cold/pressure welding, roll bonding, friction welding, friction stir welding, ultrasonic welding and explosive welding. Diffusion bonding and adhesive bonding. Joining of dissimilar materials. Analytical and numerical modelling of solid state joining processes.
Manufacturing Processes II
Material removal processes: mechanics of machining, tool geometry and materials, chip formation, tool temperature, tool wear, tool life, surface finish, machinability. Optimization of machining processes. Machine tools: generation of surfaces by machining, basic operations on shaping, slotting and planning machines, lathe, drilling and boring machines, and grinding machines. Process parameters and setups. Production machines: Capstan and turret lathes, automats, broaching machines, centreless grinding machines. Special purpose machines for thread cutting and gear cutting (hobbing and shaping). Finishing processes honing, laping burnishing and deburring. Introduction to modern machining processes: EDM, ECM, LASER, Jigs and fixtures, principles of location and clamping, synthesis of simple jigs and fixtures. Principles of assembly engineering, theory of dimensional chains, fully interchangeable and selective assembly. Introduction to Numerical Control.
Heat Transfer and Metrology Lab
Part A: Heat Transfer Determination of the thermal conductivity of a material in granular form. Determination of the total hemispherical emissivity of a surface by two methods. Study the natural convection heat transfer from a vertical tube. Study the performance of a pin fin under natural and forced convection conditions. Heat transfer through circular tube with uniform heat flow. Measurement of the forced convection heat transfer coefficient in cross-flow over a circular tube. Study the performance of a double-pipe heat exchanger under parallel and counter flow conditions. Part B: Metrology Measurements of lengths, angles, flatness, squareness, parallelism, alignment, surface finish, and errors in gears and screw threads.
Manufacturing Practice Lab
Manufacturing and fitting of a machine subassembly according to given specification by groups of students.
Materials Processing and Simulation Laboratory
Hardware and Simulation experiments in Metal forming, welding, casting and Machining Laboratories.